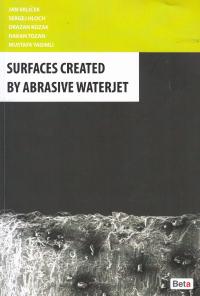
CONTENTS
NOMENCLATURE 7
ABBREVIATIONS. 11
1 INTRODUCTION. 12
2 STATE OF THE ART ANALYSIS. 14
2.1 TECHNOLOGY SET UP. 19
2.1.1 Pressure generation20
2.1.2 Abrasive delivery system.21
2.1.3 Cutting head and motion system23
2.2 FORMATION OF THE HYDROABRASIVE JET. 24
2.3 INTERACTION WITH MATERIAL.25
2.3.1 Removal processes.26
2.3.2 Surface topography. 27
2.4 CAUSES AFFECTING THE SURFACE IRREGULARITIES 30
2.5 EXAMPLE OF STATISTICAL EVALUATION. 37
2.5.1 Results and discussion.41
2.6 FUZZY AHP BASED DECISION SUPPORT SYSTEM 44
2.6.1 AHP model. .45
2.6.2 Fuzzy AHP Model .47
2.6.3 Proposed DSS and application.50
2.7 SURFACE QUALITY AND METROLOGY. 54
2.7.1 Geometrical specification of surface. 59
2.7.1.1Standards parameters59
2.7.1.2Nonstandards parameters. 61
3 SURFACE MEASUREMENT PRESENT STATE 62
3.1.1 Mechanical methods 63
3.1.2 Optical methods. 64
3.1.3 Other methods. 65
3.2 SIGNAL PROCESSING. 67
3.2.1 The classification of signals 67
5
3.2.2 Decomposition of the surface structure and topography. 69
3.2.3 Decomposition of surface structure by analysis the amplitude spec. 71
3.2.4 Autocorrelation function in decomposition and spectral analysis.74
3.3 PROBLEM DEFINITION. 76
3.4 MEASUREMENT METHODS. 78
3.4.1 Optical measurement. 78
3.4.2 The method of visualization of phase differences by defocusing79
3.4.3 The method of the lar speckle scattered light intensity. 80
3.4.4 The method of scanning of the shadow distribution on the surface 82
3.4.5 Method of the surface shadow distribution evaluation by CCD
camera84
3.4.6 The method of angle correlation of the laser speckle fields 85
3.4.7 Grid projection method86
3.4.8 Optical profilometer microprof FRT. 88
3.4.8.1 Principle of optical profilometer MicroProf. 88
4 EXPERIMENTAL ANALYSIS OF SURFACES91
4.1 TECHNICAL MATERIAL CLASSIFICATION 92
4.2 MATERIAL MACHINABILITY 93
4.3 IRREGULARITIES 95
4.4 EXPERIMENTS 96
5 RESULTS AND DISCUSSION.102
5.1 GRID PROJECTION METHOD RESULTS 102
5.2 THE RESULTS OBTAINED BY THE OPTICAL AND
CONTACT PROFILOMETER. 109
5.2.1 Statistical results 115
5.3 SHADOW DISTRIBUTION ON THE SURFACE. 121
5.4 THE METHOD OF SCANNING OF THE SHADOW
DISTRIBUTION ON THE SURFACE. 121
5.5 SHADOWS DISTRIBUTION EVALUATION BY CCD CAMERA. 127
6
5.5.1 Analysis of signals by wavelet transformation130
5.5.2 Overview of wavelet analysis 131
5.5.3 Wavelet bases and its selection134
5.5.4 Surface profile analysis and synthesis. 135
5.5.5 Results obtained by shadow method and contact profilometer. 138
5.6 COMPARISON OF RESULTS BETWEEN COMMERCIAL
METHOD AND SHADOW METHOD 148
6 PREDICTION OF THE GEOMETRICAL PARAMETERS PROPOSAL. 149
6.1 CONCEPTUAL STRUCTURE 149
6.2 PREDICTION OF DISTRIBUTION RELATIONSHIP OF
TITANIUM 155
6.2.1 Problem definition. 156
6.2.2 Findings. 158
6.2.3 Refined behaviour of surface roughness. 163
6.3 PROPOSAL OF THE OPTIMAL TRAVERSE SPEED FOR
MACHINED MATERIAL. 174
7 CONCLUSIONS. 181
REFERENCES 1
CONTENTS
NOMENCLATURE 7
ABBREVIATIONS. 11
1 INTRODUCTION. 12
2 STATE OF THE ART ANALYSIS. 14
2.1 TECHNOLOGY SET UP. 19
2.1.1 Pressure generation20
2.1.2 Abrasive delivery system.21
2.1.3 Cutting head and motion system23
2.2 FORMATION OF THE HYDROABRASIVE JET. 24
2.3 INTERACTION WITH MATERIAL.25
2.3.1 Removal processes.26
2.3.2 Surface topography. 27
2.4 CAUSES AFFECTING THE SURFACE IRREGULARITIES 30
2.5 EXAMPLE OF STATISTICAL EVALUATION. 37
2.5.1 Results and discussion.41
2.6 FUZZY AHP BASED DECISION SUPPORT SYSTEM 44
2.6.1 AHP model. .45
2.6.2 Fuzzy AHP Model .47
2.6.3 Proposed DSS and application.50
2.7 SURFACE QUALITY AND METROLOGY. 54
2.7.1 Geometrical specification of surface. 59
2.7.1.1Standards parameters59
2.7.1.2Nonstandards parameters. 61
3 SURFACE MEASUREMENT PRESENT STATE 62
3.1.1 Mechanical methods 63
3.1.2 Optical methods. 64
3.1.3 Other methods. 65
3.2 SIGNAL PROCESSING. 67
3.2.1 The classification of signals 67
5
3.2.2 Decomposition of the surface structure and topography. 69
3.2.3 Decomposition of surface structure by analysis the amplitude spec. 71
3.2.4 Autocorrelation function in decomposition and spectral analysis.74
3.3 PROBLEM DEFINITION. 76
3.4 MEASUREMENT METHODS. 78
3.4.1 Optical measurement. 78
3.4.2 The method of visualization of phase differences by defocusing79
3.4.3 The method of the lar speckle scattered light intensity. 80
3.4.4 The method of scanning of the shadow distribution on the surface 82
3.4.5 Method of the surface shadow distribution evaluation by CCD
camera84
3.4.6 The method of angle correlation of the laser speckle fields 85
3.4.7 Grid projection method86
3.4.8 Optical profilometer microprof FRT. 88
3.4.8.1 Principle of optical profilometer MicroProf. 88
4 EXPERIMENTAL ANALYSIS OF SURFACES91
4.1 TECHNICAL MATERIAL CLASSIFICATION 92
4.2 MATERIAL MACHINABILITY 93
4.3 IRREGULARITIES 95
4.4 EXPERIMENTS 96
5 RESULTS AND DISCUSSION.102
5.1 GRID PROJECTION METHOD RESULTS 102
5.2 THE RESULTS OBTAINED BY THE OPTICAL AND
CONTACT PROFILOMETER. 109
5.2.1 Statistical results 115
5.3 SHADOW DISTRIBUTION ON THE SURFACE. 121
5.4 THE METHOD OF SCANNING OF THE SHADOW
DISTRIBUTION ON THE SURFACE. 121
5.5 SHADOWS DISTRIBUTION EVALUATION BY CCD CAMERA. 127
6
5.5.1 Analysis of signals by wavelet transformation130
5.5.2 Overview of wavelet analysis 131
5.5.3 Wavelet bases and its selection134
5.5.4 Surface profile analysis and synthesis. 135
5.5.5 Results obtained by shadow method and contact profilometer. 138
5.6 COMPARISON OF RESULTS BETWEEN COMMERCIAL
METHOD AND SHADOW METHOD 148
6 PREDICTION OF THE GEOMETRICAL PARAMETERS PROPOSAL. 149
6.1 CONCEPTUAL STRUCTURE 149
6.2 PREDICTION OF DISTRIBUTION RELATIONSHIP OF
TITANIUM 155
6.2.1 Problem definition. 156
6.2.2 Findings. 158
6.2.3 Refined behaviour of surface roughness. 163
6.3 PROPOSAL OF THE OPTIMAL TRAVERSE SPEED FOR
MACHINED MATERIAL. 174
7 CONCLUSIONS. 181
REFERENCES 1